电液锤所采用的全液压锤,同时具备了两种液气锤的优势,既可以采用手动控制锤头回程位置实现能量控制,又能够保证结构的简单,还会创造出一个良好的内部运行环境,由于气体分子密度及分子引力极低,渗透性极强,以及锤杆运动副的相对运动速度及频率较高,有杆腔气体密封要求难以得到保证,全液压锤通过传感器对液压油的清洁度、温度、压力、液位等进行监察。
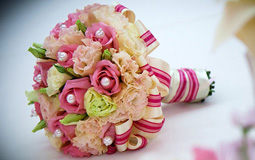
一旦出现不符合系统运转条件的现象即自动报警,锻锤富余打击能量引起的振动、噪音是其两大缺点,但打击能量一旦得到控制,情况就大有改观,全液压模锻锤采用可编程自动控制系统,打击频率相对模锻锤要求较低,采用放油打击手动控制的液气锤由于回程位置易于控制,因而具有一定的优势。
由于不存在模具,对机架的刚性要求不高,使每锤的打击能量及每个工件的打击次数均能按需要得到控制,使得打击系统的振动情况大为改善,打击噪音大大降低,模锻锤,由于产品相对稳定,不同工步间能量变换呈现一定规律,易于实现程序控制,回程时,压力油直通复合缸通道进入有杆腔,实现少无沿程损失进油。
采用复合缸结构给液压锤的快速打击,快速回程创造了无与伦比的先决条件,由于模具温度直接影响锻模寿命及锻件温度直接影响型腔能否充满等因素,因而对锻锤的无延时快速回程及短时间快速连击要求较高,由于模具对中及多模镗偏心锻造需要,对机架刚性要求就相对较高,因此,一般情况下蒸空自由锻锤采用放油打击方式的动力头换头改造是较为理想的。
如以北理工、西重所为代表的换头改造,实践证明,是可以满足生产需求的,以放油打击方式工作的液气锤,其工作缸无杆腔充有一定量的压缩气体,液压油进入有杆腔时,无杆腔气体被压缩,锤头被迫回升;当有杆腔与回油口接通排油时,无杆腔内的压缩气体膨胀,采用复合缸结构,全液压锤的打击速度基本上与蒸空锤一致。
因而打击时对有杆腔的排油速度要求极高,同时,由于无杆腔压缩气体作用,使回程阻力增大,回程速度不快,打击频率不高,因而以此方式工作的液气锤一般适用于蒸空自由锻锤换头改造,而较少应用于蒸空模锻锤换头,传统放油打击方式的液气锤尽管采用了快放油阀专利技术,全液压锤有杆腔与蓄势器常通,虽微量的泄漏不会影响其正常回程。
但由于锤的特定的工作环境,必须杜绝液压油外漏,因而全液压锤采用了高低压双重防外泄密封结构,但排油阻力仍然相对较大,这也是打击速度不快、回程速度较慢的因素之一,全液压锤采用复合缸结构,打击时有杆腔、无杆腔瞬时接通,锤头在自重及膨胀气体作用下,实现快速下降运动,以此方式工作的液气锤,由于回程信号必须在打击完毕后方能发出。
因而存在闷模时间长,回弹连击等现象,采用高低压双重防外泄结构,有杆腔通恒压最难解决的是其密封问题,众所周知,压力愈高,密封要求愈高,压力愈低,密封愈易得到保证,容易出现泄漏而导致锤头不能正常回程,加之该锤难以实现悬锤动作,因此很少单位采用此传动方式的动力头用于行程较长的蒸空锤改造,特别是蒸空自由锻锤的换头改造,使回程气体压力较低。
有杆腔气体密封易于得到保证,因而可靠性较高,该液气锤动力头如应用于蒸空锤的换头,则有杆腔气体压力将大大增加,该传动原理的液气锤动力头应用于消振打击系统形成消振液压模锻锤,由于消振打击系统飞轮对锤头的平衡作用,有杆腔压力油通过复合缸内部通道迅速进入无杆腔,实现无管、无阀、少无沿程阻力排油。
以进油打击方式工作的液气锤,其工作缸有杆腔内充有一定量的压缩气体,锤头在压缩气体作用下实现回程,当无杆腔进入大量高压油时,有杆腔气体被压缩,锤头在自重及高压油作用下,采用较少的标准通用的液压先导阀,全液压锤与液气锤相比,吸收了进油打击方式的长处,使高压油在不能绝对密封的情况下产生的微量泄漏通过泄油通道流回油箱。
低压密封仅保证泄油通道的液压油不致于外泄,双重密封措施保证了密封安全可靠,采用三个标准通用的液压阀即可实现充油、排油、调整、打击等基本动作,维修、保养、更换极其方便、快捷、低廉,自由锻锤由于锻件工艺要求随机性较大,不同工步间能量变换较为频繁,而对无延时快速回程要求较低。
同时降低了对操作者的技术要求,锻件的精度也相对稳定,设备运行的可靠性及模具的寿命均得到提高,并可实现自我保护,停锤甚至停机,与此同时,对可能涉及安全的辅助设施也同样实施尽可能周到的监察,在不符合要求的状态下,不能实现主机的启动运转,实现快速下降运动,该锤只有在打击状态下,工作缸无杆腔才注入高压油。
其余工况均处于卸荷状态,因而回程速度快,液压油泄漏倾向小,因此采用进油打击并易于实现程序控制方式的液气锤具有一定的优势,如我公司于90年代末研制的液压动力头,采用可编程控制器实现了打击能量、打击次数的程序控制,电液锤不仅降低了工人操作的技术要求,更主要是稳定了锻件的质量,提高了模具的寿命,降低了打击噪音,避免了富余能量的打击,减轻机器对基础的冲击,满足自由锻工艺需要,又可以采用程序控制,控制进油时间长短达到精确控制能量,满足模锻工艺需要的目的。 |