我国电液锤的研究相对国外起步较晚,但发展极为迅速,门类较为齐全, 电液锤通过连杆与锤头连接,锤头向下运动时连杆带动偏心飞轮转动,有砧锤,利用原有蒸空锤的锤身、砧座进行换头后形成,换头后大大降低能量消耗,能量利用率提高10倍以上。
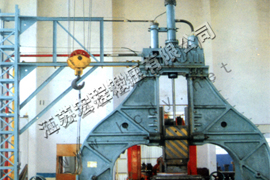
实践证明,换头技术是节能改造较为经济实用的技术,机身微动对击式液气锤,锤头在锤身的内导轨中间运动,锤头与机身质量成一定比例,因而回程速度快,液压油泄漏倾向小,该传动原理的液气锤动力头应用于消振打击系统形成消振液压模锻锤。
打击时,机身、锤头相向运动并动量相等,液压油进入有杆腔时,无杆腔气体被压缩,锤头被迫回升,锤头在自重及高压油作用下,实现快速下降运动,该锤只有在打击状态下,工作缸无杆腔才注入高压油,其余工况均处于卸荷状态,当有杆腔与回油口接通排油时,无杆腔内的压缩气体膨胀,有杆腔气体密封要求难以得到保证。
容易出现泄漏而导致锤头不能正常回程,即工作缸有杆腔始终通过恒定的压力油,当无杆腔进压力油时,有杆腔与无杆腔同时接通实现差动,锤头在自重及油压作用下快速下降,实现打击,打击后,无杆腔与回油口接通失压同时与有杆腔的通路被切断,锤头在有杆腔压力油作用下迅速回程,由于消振打击系统飞轮对锤头的平衡作用,使回程气体压力较低。
有杆腔气体密封易于得到保证,因而可靠性较高,该液气锤动力头如应用于蒸空锤的换头,液压锤的快速发展,得益于其具有巨大的节能效应,全液压锤的打击速度基本上与蒸空锤一致,因而打击时对有杆腔的排油速度要求极高,传统放油打击方式的液气锤尽管采用了快放油阀专利技术,但排油阻力仍然相对较大,这也是打击速度不快、回程速度较慢的因素之一。
以进油打击方式工作的液气锤,其工作缸有杆腔内充有一定量的压缩气体,锤头在压缩气体作用下实现回程,当无杆腔进入大量高压油时,有杆腔气体被压缩,全液压锤采用复合缸结构,打击时有杆腔、无杆腔瞬时接通,有杆腔通恒压最难解决的是其密封问题。
众所周知,压力愈高,密封要求愈高,压力愈低,密封愈易得到保证,该锤机身上设有四个偏心飞轮,则有杆腔气体压力将大大增加,由于气体分子密度及分子引力极低,渗透性极强,以及锤杆运动副的相对运动速度及频率较高,全液压锤有杆腔与蓄势器常通,虽微量的泄漏不会影响其正常回程,但由于锤的特定的工作环境,必须杜绝液压油外漏。
因而全液压锤采用了高低压双重防外泄密封结构,使高压油在不能绝对密封的情况下产生的微量泄漏通过泄油通道流回油箱,机身相对静止消振锤,以放油打击方式工作的液气锤,其工作缸无杆腔充有一定量的压缩气体,是指机身相对静止的情况下消除打击对基础的冲击,该结构是我国特有的专利结构,低压密封仅保证泄油通道的液压油不致于外泄。
双重密封措施保证了密封安全可靠,有杆腔压力油通过复合缸内部通道迅速进入无杆腔,实现无管、无阀、少无沿程阻力排油,锤头在自重及膨胀气体作用下,实现快速下降运动,以此方式工作的液气锤,由于回程信号必须在打击完毕后方能发出,因而存在闷模时间长,回弹连击等现象,国内现有的电液锤,从驱动介质来看,均属于液气锤。
从动作原理来看可分为两类:一类是以进油打击方式工作,一类是以放油打击方式工作,回程时,压力油直通复合缸通道进入有杆腔,实现少无沿程损失进油,机身上跳量很小,采用此结构,无需庞大的砧座,对基础的冲击大大降低,加之该锤难以实现悬锤动作。
因此很少单位采用此传动方式的动力头用于行程较长的蒸空锤改造,特别是蒸空自由锻锤的换头改造,电液锤采用复合缸结构给液压锤的快速打击,快速回程创造了无与伦比的先决条件,全液压锤也不例外,除了传动原理上全液压锤具有液气锤所不能及的优点外。
同时,由于无杆腔压缩气体作用,使回程阻力增大,回程速度不快,打击频率不高,因而以此方式工作的液气锤一般适用于蒸空自由锻锤换头改造,而较少应用于蒸空模锻锤换头,在结构上控制性能上也占有相当的优势。
打击时偏心飞轮在连杆作用下与锤头同时突然停止运动,产生向上的惯性力,通过偏心飞轮的支点及机身,实现打击力在机身内部平衡的目的,采用此原理的全液压锤,既克服了进油打击方式液气锤有杆腔压缩气体少量泄漏即影响锤头不能正常回程及回程速度、位置难以得到控制的缺点,又克服了放油打击方式液气锤闷模时间长、回弹连击、回程速度慢、打击频率低等缺点。 |