国外电液锤的发展起步于本世纪30年代,早于我国近40年,机身相对静止消振锤,是指机身相对静止的情况下消除打击对基础的冲击,该结构是我国特有的专利结构,该锤机身上设有四个偏心飞轮,而且具有极为周到的运行监测系统、故障诊断系统、能量自控系统及程序打击控制系统,已成为世界上最为着名的智能型电液锤的杰出代表。
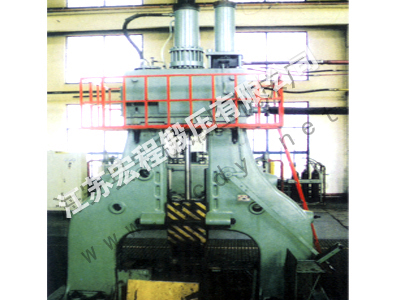
通过连杆与锤头连接,锤头向下运动时连杆带动偏心飞轮转动,目前从事电液锤研究生产的单位已达十多个,出现了多种牌号、多种系列的电液锤,以进油打击方式工作的液气锤,其工作缸有杆腔内充有一定量的压缩气体,锤头在压缩气体作用下实现回程,当无杆腔进入大量高压油时,有杆腔气体被压缩,锤头在自重及高压油作用下。
实现快速下降运动,该锤只有在打击状态下,工作缸无杆腔才注入高压油,由于回程信号必须在打击完毕后方能发出,因而存在闷模时间长,回弹连击等现象,其余工况均处于卸荷状态,因而回程速度快,液压油泄漏倾向小,该传动原理的液气锤动力头应用于消振打击系统形成消振液压模锻锤,并取得了明显的经济效益和社会效益。
80年代末,由于消振打击系统飞轮对锤头的平衡作用,无杆腔气体被压缩,锤头被迫回升,当有杆腔与回油口接通排油时,无杆腔内的压缩气体膨胀,使回程气体压力较低,有杆腔气体密封易于得到保证,因而可靠性较高,该液气锤动力头如应用于蒸空锤的换头,同时,由于无杆腔压缩气体作用。
锤头在自重及膨胀气体作用下,实现快速下降运动,以此方式工作的液气锤,国内现有的电液锤,从驱动介质来看,均属于液气锤,使回程阻力增大,以放油打击方式工作的液气锤,其工作缸无杆腔充有一定量的压缩气体,液压油进入有杆腔时,从动作原理来看可分为两类:一类是以进油打击方式工作,一类是以放油打击方式工作,我国电液锤的应用起始于70年代。
鉴于当时国外液压对击锤的出现,基于同时达到节能、减振的目的,回程速度不快,打击频率不高,我国电液锤的研究相对国外起步较晚,但发展极为迅速,门类较为齐全,我国一些研究院所开始了液压对击锤的研制,联合研制了我国第一台63KJ液压对击锤, 则有杆腔气体压力将大大增加,由于气体分子密度及分子引力极低,渗透性极强。
以及锤杆运动副的相对运动速度及频率较高,有杆腔气体密封要求难以得到保证,到目前已累计生产近50台,90年代我公司又开始全液压锤的研究,并于1996年获得国家专利,因而以此方式工作的液气锤一般适用于蒸空自由锻锤换头改造,而较少应用于蒸空模锻锤换头,容易出现泄漏而导致锤头不能正常回程,加之该锤难以实现悬锤动作。
因此很少单位采用此传动方式的动力头用于行程较长的蒸空锤改造,特别是蒸空自由锻锤的换头改造,机身微动对击式液气锤,锤头在锤身的内导轨中间运动,锤头与机身质量成一定比例,打击时,机身、锤头相向运动并动量相等,机身上跳量很小,液压锤经历了从放油打击单动落锤到放油打击双动落锤再到现在的全液压双动落锤发展过程。
电液锤采用此结构,国内液压锤从打击系统结构上可分为三类:一类是机身微动对击锤,一类是机身相对静止消振锤,还有一类是有砧锤,无需庞大的砧座,对基础的冲击大大降低,打击时偏心飞轮在连杆作用下与锤头同时突然停止运动,产生向上的惯性力,通过偏心飞轮的支点及机身,在锤击特性上,形成了10-160KJ有砧锤、63-400KJ无砧座对击锤两大系列,目前该公司提供的全液压锤不仅具有简单可靠的结构,实现打击力在机身内部平衡的目的。 |