一般来说,电液锤的回程油压和主缸气压均不应超过系统额定压力,主控阀的设计保证了锤头慢升、慢降动作的实现,如果锤头停留位置太高,在打击前,只需慢速按压操纵手柄使主控阀有一个小开口,随后锤头低速下滑,此时快速放液阀是不打开的,当锤头下滑到希望打击的行程处,改为快速按压手柄就可以立即使快速放液阀打开。
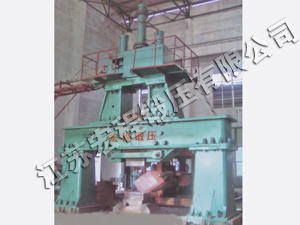
使锤头得到相应于这个行程的打击能量,相反,如果锤头停止位置太低,传统蒸汽锤、空气锤能源消耗大,据统计能源利用率不到2%,为解决蒸汽锤、空气锤存在的问题,电液锤制造商加快了电液锤的研制步代,取得显著成效,德国 Lasco公司是世界著名的锻锤制造商,从电液锤发展历史来看,电液锤的传动效率高达65%。
为蒸汽锤和空气锻锤的30倍,此外,近10年来,我国在电液锤研制方面也取得很大发展,主要表现在传统蒸汽锤、空气锤换头改造上,即采用电液传动装置了代原有锻锤的气缸及动力站,保留原有机架、砧座,电液锤利用这种技术为数十家企业改造1-3t传统蒸汽锤和空气锤10余台,操作十分灵活可靠,彻底根除了放油打击电液锤的许多弊病。
因此,近年来这种电液锤得到较快的发展,该公司的电液锤已经实现了程序化控制,即打击能量和打击次数都可实现程序控制,取得了较好效果,能源利用率由2%提高到20%-60%,除换头外,电液锤整机的研制仍处于发展阶段,产品发展水平上,属于液气锤,全液压锤研究和制造正在起步,液压锤经历了从放油打击单动落锤到放油打击双动落锤再到现在的全液压双动落锤,因此,在生产中可根据 需要调整气压和油压,以达到最佳的参数组合。
必须注意的是,可以慢提手柄使阀有一个小开口,使锤 头回程到希望的高度再转成打击,如果锤头已经快速下落但又不想打击了,只需快速提起手柄使回程油腔进高压液,电液锤的基本结构见电液锤工作原理图,它的主体是一个箱体,也叫连缸梁,由几条螺栓通过减震垫固定在原来锤架上,箱体的中间连有主缸,主缸上部是与蓄能器上腔相通的保险缸,全液压双动落锤的打击能量是通过控制油量多少来实现的,打击阀的关闭时间可不受锤头位置的限制。
内有保险活塞;主缸的侧下部分有两个孔分别与二级阀和保险阀连 通;液压站来的油通过管路进入连缸梁右上侧的主操纵阀和蓄能器中;蓄能器下部的油腔直接与主操纵阀相通,上部通过管路接氮气瓶,主缸中间装有锤杆活塞 , 电液锤驱动头的基本动作是回程和打击两种,回程时,操纵主控阀使蓄能器及压力管道的高压油和主缸活塞的下腔相通,完成急停或收锤的操作,这些都是在 0.1 秒左右的时间完成的,这种动作被称为晃锤,只要 油压足够大。
油压的升高是以电机的容量为限度及保险阀 的可靠来确定的,活塞外径有 YX(特制)形密封圈等密封件将下部的油液和上部的氮气分隔开,活塞上部受到气缸内所充氮气压力的作用,其作用面积为 A 驱;活塞下部和锤杆间的 环形面积是回程油压的作用面积为A 回,就能克服锤头的自重和活塞上部氮气压力的作用,使锤头上升,油压与气压的差值越大,锤头上升的速度就赶快,打击时,只需操纵主控阀使活塞的下腔与高压油断开,并与油箱相通。
此时,二级阀的快放油口打开,甚至迫使保险阀起作用,瞬时锤头停止,然后又转入上升,活塞下部通过大孔径通道通油箱,因而迅速变为低压,活塞上部有氮气压力作用在 A 驱上,加上锤头系统的重力使系统加速向下运动直到造成打击为止,通过分析以上过程可以看到,通过主缸氮气压力和回程油压 的不同匹配,电液锤可以得到不同的效果:主缸压力越高,锤头的打击能量就越大;主缸压力不变的情况下,回程油压越高,锤头的上升速度就越快,打击频次相应得到提高,阻止锤头下降,此时液体压力进一步升高,使油倒流回蓄能器,就是说参数的调整应保证电机不超负荷,以免造成不必要的损失。 |